

So far, this document has addressed only what are called single-ended incremental quadrature encoders.
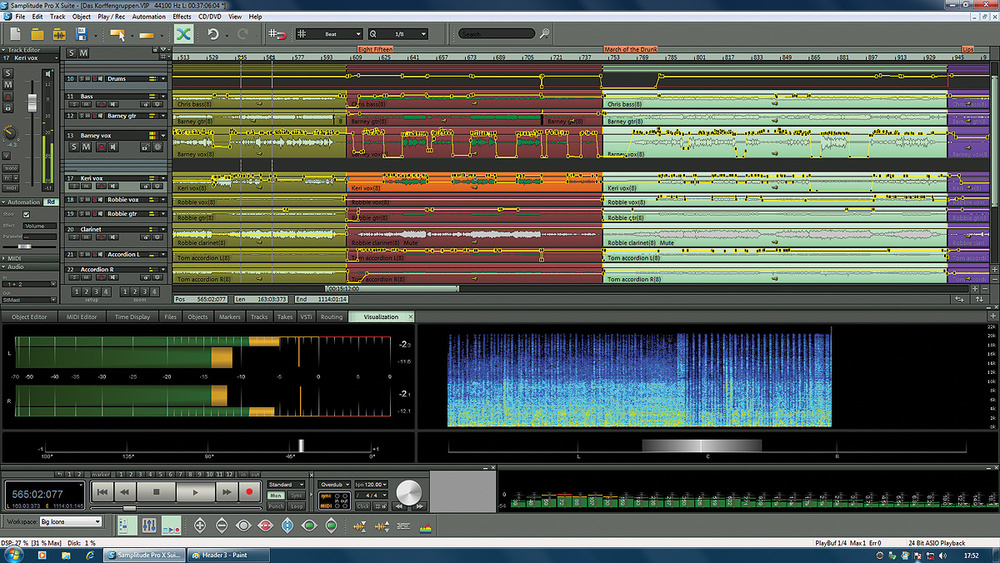
In the majority of encoders, this signal is called the Z-Terminal or the index. You can use this single pulse for precise determination of a reference position. In addition, some quadrature encoders include a third output channel – called a zero or reference signal – which supplies a single pulse per revolution. Linear encoders work under the same principle as rotary encoders except that instead of a rotating disk, there is a stationary opaque strip with transparent slits along its surface, and the LED-detector assembly is attached to the moving body. This means that these encoders can provide 3.6 deg of resolution for the encoder with 100 segments and 0.06 deg of resolution for the encoder with 6,000 segments. This generates square-wave pulses, which can then be interpreted into position or motion.Įncoders usually have from 100 to 6,000 segments per revolution. As the disk rotates, the opaque segments block the light and, where the glass is clear, light is allowed to pass. The disk, which is mounted on the rotating shaft, has patterns of opaque and transparent sectors coded into the disk. Figure 1 shows the fundamental components of a rotary encoder, which consists of a light-emitting diode (LED), a disk, and a light detector on the opposite side of the disk. Rotary encoders are used to measure the rotational motion of a shaft.
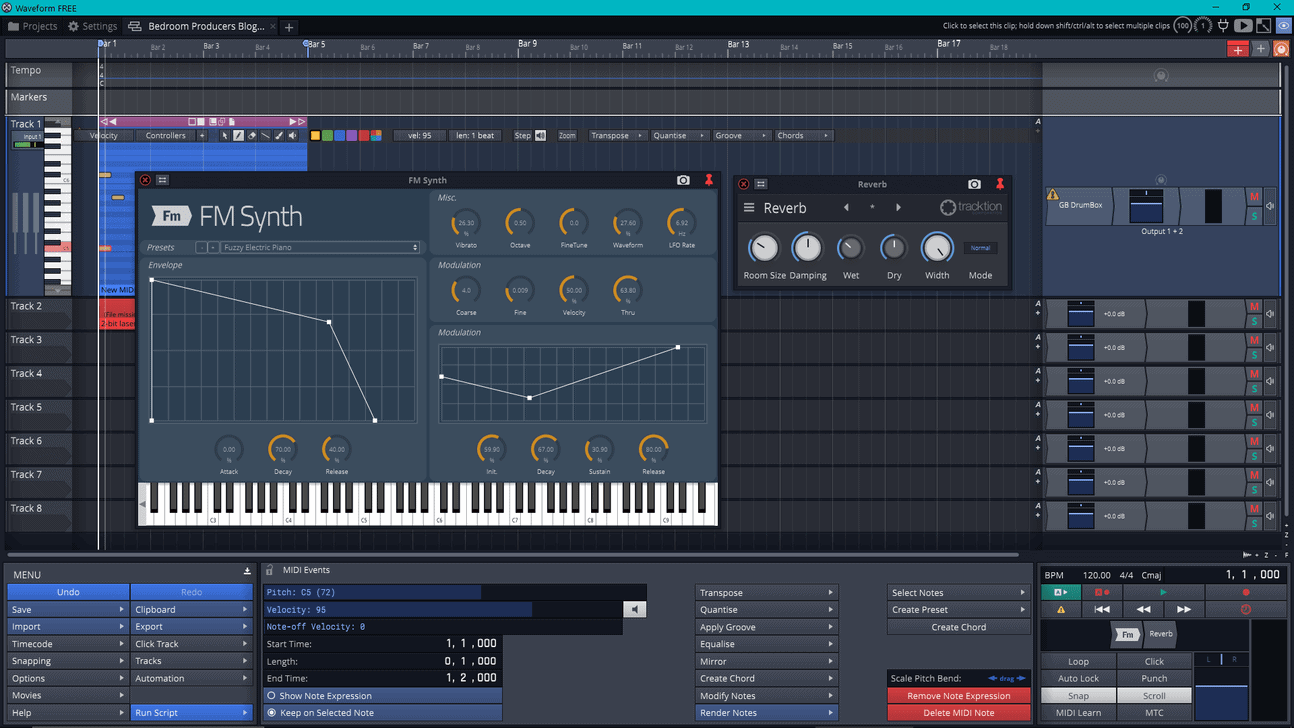
Most encoders use optical sensors to provide electrical signals in the form of pulse trains, which can, in turn, be translated into motion, direction, or position. This document describes encoder theory, the basics of measuring an encoder, and options for measuring encoders use NI hardware.Īn encoder is an electromechanical device that can measure motion or position.
